การชุบผิวแข็งด้วยการทำคาร์เบอร์ไรซิง |
|
เรียบเรียงโดย อุษณีย์ กิตกำธร |
|
เนื่องจากชิ้นส่วนเครื่องจักรบางชิ้นส่วนต้องการความแข็งผิวสูงเพื่อให้ทนต่อการสึกหรอได้ดี ในขณะที่ต้องการความเหนียวและสามารถดูดซับแรงได้สูงด้วยเช่นกัน จึงได้มีการนำเอาเหล็กกล้าคาร์บอนต่ำซึ่งมีความเหนียวสูงมาปรับปรุงให้บริเวณผิวมีความแข็งสูงขึ้น อย่างไรก็ตามเหล็กกล้าที่มีคาร์บอนต่ำนั้นชุบผิวแข็งโดยตรงเลยไม่บังเกิดผล เนื่องจากมีคาร์บอนต่ำเกินไปจึงชุบแล้วไม่ได้มาร์เทนไซต์ ดังนั้นจึงต้องมีการเติมคาร์บอนเข้าไปที่ชั้นผิวของเหล็กกล้าที่มีคาร์บอนต่ำก่อน เมื่อชั้นผิวมีคาร์บอนเพิ่มสูงขึ้นแล้ว การชุบแข็งทั้งชิ้นงานในภายหลังจะส่งผลให้ได้มาร์เทนไซต์ที่ชั้นผิวในขณะที่ภายในยังคงโครงสร้างเฟอร์ไรต์ที่มีความเหนียวสูงไว้ เรียกวิธีการเติมคาร์บอนที่ชั้นผิวเหล็กว่า คาร์เบอร์ไรซิง (carburizing) โดยปกติแล้วการทำคาร์เบอร์ไรซิงให้ได้ผลดีนั้นควรทำกับเหล็กกล้าที่เจือธาตุผสมเล็กน้อย เช่น Cr Ni Si และ Mo เป็นต้น เนื่องจากการมีเพียงคาร์บอนอย่างเดียวนั้น ความสามารถในการชุบแข็งจะไม่สูงพอ |
|
ค่าความแข็งของชิ้นงานเหล็กที่ผ่านการทำคาร์เบอร์ไรซิงแล้วชุบแข็งและอบคืนไฟแล้วจะมีค่าสูงสุดที่ผิวและลดลงตามความลึกเข้าไปในชิ้นงาน นอกจากนี้ความเค้นแรงอัดเหลือค้างหลังจาการชุบแข็งก็จะช่วยเพิ่มความต้านทานการล้าให้กับชิ้นงานอีกด้วย |
|
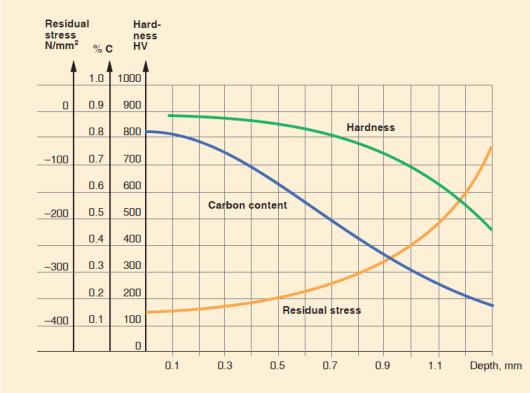 |
ความเข้มข้นของคาร์บอนในหน่วยเปอร์เซ็นต์โดยน้ำหนัก ความแข็ง และความเค้นตกค้าง ที่ตำแหน่งลึกลงไปจากชั้นผิว
Linde booklet: Furnace Atmosphere No.1 Gas carburizing and carbonitriding. Special Edition available from http://heattreatment.linde.com/international/web/lg/ht/like35lght.nsf/docbyalias/homepage |
|
วิธีการทำคาร์เบอร์ไรซิง อาจแบ่งออกได้ตามสถานะหรือชนิดของแหล่งจ่ายคาร์บอน เช่น แก๊สคาร์เบอร์ไรซิง แพ็คคาร์เบอร์ไรซิง และลิควิดคาร์เบอร์ไรซิง โดยวิธีที่นิยมใช้ในอุตสาหกรรมมากที่สุดคือ แก๊สคาร์เบอร์ไรซิง เนื่องจากควบคุมพารามิเตอร์ในการทำคาร์เบอร์ไรซิงได้ง่ายและแน่นอนกว่า รวมทั้งยังเกิดมลพิษและกากของเสียน้อยกว่า
|
|
เนื่องจากการเติมคาร์บอนเข้าไปที่ชั้นผิวนั้นต้องอาศัยการแพร่ของคาร์บอนซึ่งจัดเป็นกระบวนการที่ต้องอาศัยความร้อนและเวลา ดังนั้นจึงต้องทำที่อุณหภูมิสูงเป็นเวลาที่เหมาะสม รวมทั้งต้องควบคุมศักย์คาร์บอนที่ผิวนอกสุดของชิ้นงานเหล็กด้วย ซึ่งโดยปกติศักย์คาร์บอนที่ใช้จะอยู่ที่ 0.8%C ส่วนอุณหภูมิจะอยู่ที่ประมาณ 900-950 องศาเซลเซียส และเวลาประมาณ 4-8 ชั่วโมง ขึ้นกับความหนาของชั้นผิวแข็งที่ต้องการ
|
|
ระหว่างการทำคาร์เบอร์ไรซิง ศักย์คาร์บอนในบรรยากาศและที่ผิวนอกสุดจะถูกรักษาไว้ให้คงที่ และเนื่องจากค่าศักย์คาร์บอนที่ผิวนอกนั้นสูงกว่าที่เนื้อในของชิ้นงาน อะตอมของคาร์บอนจึงแพร่เข้าสู่ชิ้นงาน โดยความเข้มข้นของคาร์บอนในชิ้นงานจะเปลี่ยนแปลงไปเมื่อเวลาในการทำคาร์เบอร์ไรซิงนานขึ้น ดังแสดงในภาพ โดยความสัมพันธ์ระหว่างระยะลึกที่ต้องการให้มีความเข้มข้นของคาร์บอนที่กำหนด (x) และ เวลาที่จำเป็นต้องใช้ (t) ภายใต้การทำคาร์เบอร์ไรซิงด้วยศักย์คาร์บอนคงที่และอุณหภูมิคงที่ คือ
|
x=k√t |
|
โดยค่า k นั้นขึ้นอยู่กับ |
1) ศักย์คาร์บอนในการทำคาร์เบอร์ไรซิง |
2)%C ในเหล็กเริ่มต้น |
3) อุณหภูมิในการทำคาร์เบอร์ไรซิ |
ดังนั้นหากมีการเปลี่ยนแปลงพารามิเตอร์ตัวใดตัวหนึ่งในสามตัว ค่า k จะเปลี่ยนไป |
|
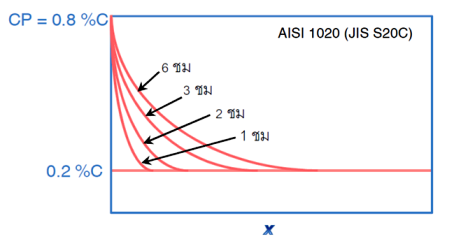 |
ความเข้มข้นของคาร์บอนที่ตำแหน่งลึกลงไปจากชั้นผิวภายหลังคาร์เบอร์ไรซิงด้วยเวลาต่างๆ กัน |
|
---------------------------------------------- |
|
การทำคาร์เบอร์ไรซิงด้วยแก๊ส |
|
ในกระบวนการคาร์เบอร์ไรซิงด้วยแก๊สนั้นแหล่งจ่ายคาร์บอนอยู่ในสถานะแก๊ส เรียกกันว่า อาร์เอ็กซ์แก๊ส (RX-gas) หรือ เอ็นโดเทอร์มิคแก๊ซ (endothermic gas) หรือแคริเออร์แก๊ส (carrier gas) โดยเป็นแก๊สผสมที่มีส่วนผสมระหว่าง CO CO2 H2 N2 และ CH4 แก๊สผสมเหล่านี้ได้จากการเผาไหม้แบบไม่สมบูรณ์ของไฮโดรคาร์บอนแก๊ส เช่น โพรเพน บิวเทน เป็นต้น ในห้องเผาไหม้ที่มีแคตาลิสต์ NiAl บรรจุอยู่ภายใน การใช้สารตั้งต้นเป็นไฮโดรคาร์บอนต่างชนิดกันก็จะผลิตออกมาเป็นคาร์เบอร์ไรซิงแก๊สได้ในปริมาณที่แตกต่างกันนอกจากนี้ก็ยังมีการก็อาจใช้สารตั้งต้นเป็นเมทานอลก็ได้เช่นกัน แต่หลักการสร้างเอ็นโดเทอร์มิคแก๊ซก็จะแตกต่างออกไปเล็กน้อยกัน |
การควบคุมบรรยากาศนั้นเป็นเรื่องสำคัญมาก CO และ CH4 เป็นแก๊สที่สามารถจ่ายคาร์บอนให้กับชิ้นงานได้ดังปฏิกิริยา |
2CO = C (in austenite) + CO2 -----------(1) |
CO = C + 1/2O2 ---------------------------- (2) |
CH4 = C (in austenite) + 2H2 ----------- (3) |
CO + H2 = C(in austenite) + H2O-------(4) |
โดยปฏิกิริยาที่ 1 และ 4 เป็นปฏิกิริยาหลักที่เกิดขึ้นในการทำคาร์เบอร์ไรซิงด้วยแก๊ส ซึ่งนอกจากการจ่ายคาร์บอนให้เหล็กแล้วยังได้ CO2 และ H2O มาด้วย ทั้งนี้หากมี CO2 และ H2O มากเกินสมดุลก็จะเกิดปฏิกิริยาย้อนกลับ ทำให้คาร์บอนที่ผิวเหล็กลดลง เรียกว่า ดีคาร์เบอร์ไรเซชัน (decarburization) ทั้งนี้ปริมาณ CO2 ที่เพิ่มขึ้นเพียงเล็กน้อย ต้องใช้ CO เป็นจำนวนมากในการสร้างสมดุลเพื่อรักษาศักย์คาร์บอนที่ผิวไว้ โดยสามารถคำนวณได้ตามหลักเทอร์โมไดนามิกส์ |
การผสมแก๊สไฮโดรคาร์บอน หรือที่เรียกว่าเอ็นริชแก๊ส (enriched gas ) ก็มีจุดประสงค์เพื่อเพิ่มประสิทธิภาพการทำคาร์เบอร์ไรซ์ของเอ็นโดแก๊ส เนื่องจากแก๊สไฮโดรคาร์บอนจะทำปฏิกิริยากับ CO2 และ H2O ให้ CO ดังปฏิกิริยา |
การควบคุมบรรยากาศการทำคาร์เบอร์ไรซิงให้ได้ผลดีนั้น ใช้การควบคุมศักย์คาร์บอนผ่านการควบคุมอัตราส่วน CO/CO2 และ H2/H2O |
|
---------------------------------------------- |
|
ศักย์คาร์บอน (carbon potential) |
|
ในระหว่างการทำคาร์เบอร์ไรซิงปฏิกิริยาที่เกิดขึ้นได้เร็วที่สุด คือปฏิกิริยา |
CO + H2 = C(in austenite) + H2O |
ซึ่งค่าคงที่ของปฏิกิริยาที่สภาวะสมดุลคือ |
K4=(aC∙P(H2O))/(PCO ∙PH2) |
|
ทั้งนี้ค่าคงที่ที่สภาวะสมดุลนั้นขึ้นกับอุณหภูมิ ตามความสัมพันธ์ log K4 = -7.494+7130/T ดังนั้นค่า aC หรือแอคติวิตี้ของคาร์บอนในบรรยากาศก็จะขึ้นอยู่กับ PCO PH2และ PH2O โดยถ้าแอคติวิตี้ของคาร์บอนในบรรยากาศสูงกว่าของคาร์บอนในเหล็ก ก็จะเกิดการถ่ายโอนคาร์บอนเข้าไปที่ผิวเหล็ก |
เนื่องจาก aC ถูกควบคุมโดยการคุม PCO PH2 และ PH2O) ดังนั้นการวัดจุดน้ำค้าง หรือดิวพ้อยต์ จึงเป็นวิธีการหนึ่งในการตรวจวัดศักย์คาร์บอนของบรรยากาศได้ อย่างไรก็ตามวิธีที่นิยมในปัจจุบันคือการวัดระดับออกซิเจนด้วยหัววัดออกซิเจน และการวัดระดับ CO2 ด้วยอินฟาเรดเซ็นเซอร์ ซึ่งการตรวจวัดด้วยวิธีการทั้งสองนั้น คิดจากสมดุลเคมีของปฏิกิริยาการแตกตัวของคาร์บอนมอนอกไซด์ 2 ปฏิกิริยาคือ |
2CO = C + CO2 |
CO = C + 1/2O2 |
ซึ่ง aC =(K2 ∙P2CO)/PCO2) และ aC = (K3 PCO)/(P(O2)1/2) ดังนั้นการควบคุมระดับ PCO หรือ P(O2) ก็ใช้ในการควบคุมแอคติวิตี้ของคาร์บอนในบรรยากาศได้เช่นกัน |
ในทางปฏิบัตินิยมใช้ศักย์คาร์บอน (carbon potential, CP) แทนแอคติวิตี้ โดยศักย์คาร์บอน หมายถึง ระดับเปอร์เซ็นต์โดยน้ำหนักของคาร์บอนในเหล็กที่จะมีอยู่ภายใต้สภาวะสมดุลร่วมกับแก๊ส พูดง่ายๆ คือในแก๊สที่มีแอคติวิตี้ของคาร์บอนเท่ากับค่าหนึ่งแล้วเหล็กที่อยู่ด้วยกันในสมดุลนั้นจะมีเปอร์เซ็นต์คาร์บอนเท่ากับค่าศักย์คาร์บอน ซึ่งศักย์คาร์บอนมีความสัมพันธ์กับแอคติวิตี้ตามสมการ |
aC=γ°XC |
เมื่อ XC คือสัดส่วนโดยโมลของคาร์บอน ซึ่งสามารถคำนวณกลับให้เป็นเปอร์เซนต์คาร์บอนโดยน้ำหนักได้ ส่วน γ° คือค่าคงที่ซึ่งขึ้นกับอุณหภูมิ |
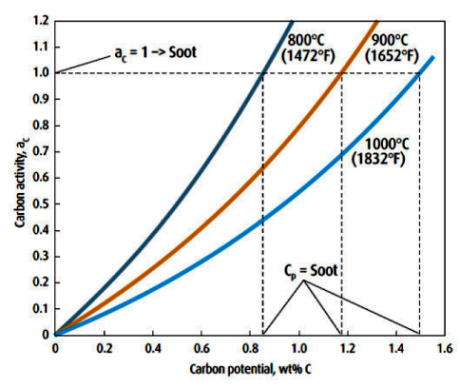 |
แอคติวิตีของคาร์บอนที่ศักย์คาร์บอนต่างๆ |
|
---------------------------------------------- |
|
การลดเวลาในการทำคาร์เบอร์ไรซิง |
|
ในการทำคาร์เบอร์ไรซิงนั้นมีจุดประสงค์เพื่อการเพิ่มคาร์บอนที่ชั้นผิวเพื่อที่จะชุบแข็งต่อไปได้ ทั้งนี้ปริมาณคาร์บอนสูงสุดที่ผิวไม่ควรสูงเกินกว่า 0.8% เนื่องจากคาร์บอนที่สูงเกินไปเมื่อชุบแข็งแล้วจะเกิดออสเทนไนต์เหลือค้างมาก การควบคุมให้คาร์บอนที่ผิวไม่เกิน 0.8% นั้นก็อาจทำได้โดยการรักษาศักย์คาร์บอนของบรรยากาศให้เท่ากับ 0.8 ตลอดระยะเวลาการทำคาร์เบอร์ไรซิง อย่างไรก็ตามหากต้องการลดเวลาช่วงการทำคาร์เบอร์ไรซิงก็สามารถทำได้โดยการเพิ่มศักย์คาร์บอนให้สูงขึ้น เช่น 1.0 หรือ 1.1 เพื่อเร่งการเติมคาร์บอนเข้าไปในชั้นผิว หลังจากนั้นค่อยลดศักย์คาร์บอนลงมา ให้ต่ำลงเป็น 0.8 เพื่อให้คาร์บอนส่วนเกินที่ผิวนอกของเหล็กลดลงกลับมาอยู่ที่ 0.8% ส่วนอุณหภูมิในการทำคาร์เบอร์ไรซิงนั้นควรอยู่ที่ประมาณ 900-950°C และเมื่อได้ปริมารคาร์บอนที่ชั้นผิวตามต้องการแล้วก็จะลดอุณหภูมิลงมาที่ช่วงอุณหภูมิที่เหมาะสมในการชุบแข็งของเหล็กกล้าที่มีคาร์บอนประมาณ 0.8% นั่นคือประมาณ 800°C แล้วจึงชุบในน้ำมัน จากนั้นก็นำไปอบคืนไฟต่อไปเพื่อให้ได้ความแข็งผิวตามต้องการ |
|
 |
การควบคุมอุณหภูมิและศักย์คาร์บอนในการทำคาร์เบอร์ไรซิงแบบสองขั้น |
|
---------------------------------------------- |
|
การพิจารณาเลือกสภาวะในการทำคาร์เบอร์ไรซิง |
|
สำหรับการเลือกสภาวะในการทำคาร์เบอร์ไรซิงนั้น โดยหลักคือต้องเริ่มพิจารณาจากความเค้นที่เกิดขึ้นกับชิ้นงานดังกล่าวขณะนำไปใช้งาน หากพิจารณาจากค่าความเค้นที่เกิดขึ้น ณ ตำแหน่งต่างๆ ของชิ้นงาน ชิ้นงานจะใช้งานได้โดยไม่เกิดความเสียหายถ้าความเค้นที่เกิดขึ้นนั้นต่ำกว่าความเค้นแรงดึงหรือความเค้นจุดคราก ถ้าเป็นกรณีของการรับแรงกระทำในลักษณะรอบซ้ำๆ ก็จะพิจารณาจากขีดจำกัดความทนทานต่อการล้า (endurance limit) ซึ่งคือค่าความเค้น ที่วัสดุดังกล่าวสามารถรับได้โดยไม่ก่อให้เกิดการแตกหักแม้ว่าจะเกิดความเค้นเป็นรอบซ้ำๆ เกินกว่า 1,000,000 รอบ ยกตัวอย่างเช่น เพลาทรงกระบอกซึ่งระหว่างการใช้งานจะเกิดความเค้นเป็นรอบซ้ำๆ โดยมีความเค้นสูงสุดที่ตำแหน่งต่างๆ ลึกเข้าไปยังใจกลางเพลาดังแสดงในภาพ หากค่าขีดจำกัดความทนทานต่อการล้าที่ตำแหน่งลึกเข้าไปยังใจกลางเพลาทุกๆจุดสูงกว่าความเค้นขณะใช้งาน ชิ้นงานดังกล่าวก็จะไม่เกิดความเสียหายภายใต้อายุการใช้งานที่ออกแบบไว้ทั้งนี้สามารถประมาณค่าขีดจำกัดความทนทานต่อการล้าได้จากค่าความเค้นแรงดึงสูงสุดและค่าความแข็ง ดังนั้นจึงสามารถใช้ค่าความแข็งผิว และความลึกผิวแข็ง ในการตรวจสอบคุณภาพงานอบชุบได้ |
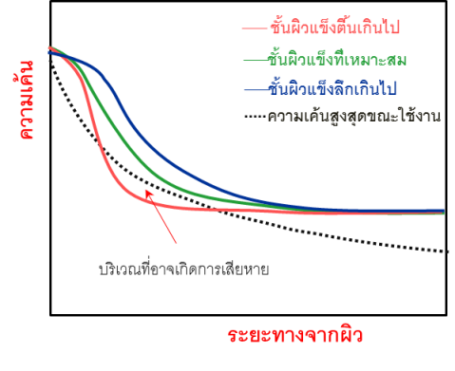 |
ความเค้นล้าที่เกิดขึ้นขณะใช้งานและความเค้นล้าสูงสุดที่ตำแหน่งต่างๆในชั้นผิวแข็ง |
|
การประมาณค่าความต้านทานแรงดึงสูงสุดเหล็กกล้าจากค่าความแข็งสามารถประมาณได้จากความสัมพันธ์อย่างง่ายคือ |
|
ถ้าค่าความแข็งสูงกว่า 175 HB แล้ว ค่า UTS = 3.55 x HB |
ถ้าค่าความแข็งต่ำกว่า 175 HB แล้ว ค่า UTS = 3.38 x HB |
|
ส่วนขีดจำกัดความทนทานต่อการล้าของเหล็กกล้านั้นอยู่ที่ประมาณ 50% ของค่าความต้านทานแรงดึงสูงสุด ยกตัวอย่างเช่น ที่ผิวต้องการให้มีขีดจำกัดความทนทานต่อการล้าคือ 1000 MPa ค่าความต้านทานแรงดึงควรจะอยู่ที่ประมาณ 2000 MPa ค่าความแข็งผิวก็น่าจะอยู่ที่ประมาณ 560 HB (หรือ ประมาณ 55 HRC หรือ 595 HV) ส่วนที่ตำแหน่งลึกเข้าไป 0.6 mm ต้องการให้มีขีดจำกัดความทนทานต่อการล้าคือ 800 MPa ค่าความต้านทานแรงดึงควรจะอยู่ที่ประมาณ 1600 MPa และค่าความแข็งที่ตำแหน่งนี้ก็น่าจะอยู่ที่ประมาณ 450 HB (หรือ ประมาณ 48 HRC หรือ 484 HV ) ซึ่งในการอบชุบก็จะตั้งเป็นเกณพ์ในการกำหนดคุณภาพคือต้องมีความแข็งผิว 55-56 HRC และ มีความลึกผิวแข็ง ณ 513 HV เท่ากับ 0.6 mm หรือมากกว่า เป็นต้น |
|
อ้างอิง |
|
[1] George E. Totten. Steel Heat Treatment Handbook : Metallurgy and Technologies, CRC Press, USA 2006 |
[2] Heat Treater’s Guide: Practice and Procedure for Iron and Steel. ASM International 2nd edition, USA 1995 |
[3] Linde booklet: Furnace Atmosphere No.1 Gas carburizing and carbonitriding. Special Edition available from |
http://heattreatment.linde.com/international/web/lg/ht/like35lght.nsf/docbyalias/homepage |
[4] Linde booklet: Furnace Atmosphere No.2 Neutral hardening and annealing. Special Edition available from |
http://heattreatment.linde.com/international/web/lg/ht/like35lght.nsf/docbyalias/homepage |
[5] Linde booklet: Furnace Atmosphere No.3 Nitriding and nitocarburizing. Special Edition available from http://heattreatment.linde.com/international/web/lg/ht/like35lght.nsf/docbyalias/homepage |