ความสามารถในการชุบแข็ง (Hardenability) |
|
เรียบเรียงโดย อุษณีย์ กิตกำธร |
|
ความสามารถในการชุบแข็ง มีความหมายรวมสองนัยคือ ความสามารถของเหล็กในการเพิ่มความแข็งได้ถึงค่าความแข็งสูงสุดที่เป็นไปได้และการกระจายตัวของค่าความแข็งตลอดความหนาของชิ้นงาน ค่าความแข็งสูงสุดที่เป็นไปได้นั้นขึ้นกับปริมาณคาร์บอนในออสเทนไนต์เป็นสำคัญ ในขณะที่การกระจายตัวของค่าความแข็งตลอดความหนาของชิ้นงานนั้นขึ้นอยู่กับ ปริมาณคาร์บอนและธาตุผสมอื่นๆ ขนาดเกรนของออสเทนไนต์ และ ความรุนแรงของการชุบ (สารชุบและการหมุนเวียนของสารชุบ) ดังนั้นเหล็กกล้าชนิดใดที่มีความสามารถในการชุบแข็งสูงจะหมายถึงสามารถชุบแข็งแล้วได้ค่าความแข็งสูงสุดที่ผิวและค่าความแข็งในส่วนที่ลึกเข้ามานั้นลดลงเล็กน้อยตามระยะลึกเข้าไปใจกลางชิ้นงาน ส่วนเหล็กกล้าชนิดใดที่มีความสามารถในการชุบแข็งต่ำอาจหมายถึงชุบแข็งแล้วไม่ได้ความแข็งสูงสุด หรือชุบแข็งแล้วได้ความแข็งสูงสุดเฉพาะที่ผิวแต่ค่าความแข็งในส่วนที่ลึกเข้ามานั้นลดลงมากตามระยะลึกเข้าไปใจกลางชิ้นงาน |
|
การตรวจสอบความสามารถในการชุบแข็งของเหล็กกล้าชั้นคุณภาพต่างๆ อาจใช้การทดสอบที่เรียกว่า “Jominy End Quench Test” ซึ่งเป็นการทดสอบที่ป็นที่ยอมรับตามมาตรฐานหลายมาตรฐานรวมไปถึงมาตรฐานนานาชาติ ลักษณะของการทดสอบอธิบายแบบง่ายๆ คือ |
|
1. นำแท่งเหล็กทรงกระบอกขนาดเส้นผ่านศูนย์กลาง 25 มม. ยาว 100 มม. ที่ผ่านการอบให้เป็นออสเทนไนต์เป็นเวลา 30 นาที ไปแขวนไว้ในแนวตั้งบนแท่น |
2. จากนั้นปล่อยน้ำพุที่มีการติดตั้งตามกำหนดมาตรฐานให้พุ่งขึ้นมาจากด้านล่างเพื่อทำให้เหล็กเกิดการเย็นตัวเกือบจะในทิศทางเดียว กล่าวคือความร้อนส่วนใหญ่ถูกดึงออกจากชิ้นงานที่ปลายด้านล่าง ดังนั้นอัตราการเย็นตัวสูงสุดอยู่ที่ปลายล่าง และอัตราเย็นตัวจะลดลงตามระยะที่ขยับจากปลายขึ้นมา |
3. เมื่อชิ้นทดสอบเย็นตัวลงถึงอุณหภูมิห้องก็นำไปกลึงปาดด้านข้างสองด้านขนานกันโดยปาดลึกเข้าไปประมาณ 0.45 มม. |
4. วัดค่าความแข็งร็อกเวลล์ C บนผิวที่ปาดมา โดยให้วัดที่ปลายแท่งแล้วเว้นระยะการวัดจากปลายแท่งทุกๆ 1/16 นิ้ว ถ้าใช้หน่วยมิลลิเมตร ก็ให้วัดทุกๆ 2 มม. เป็นระยะประมาณ 20 ถึง 40 มม. พิจารณาตามการเปลี่ยนแปลงของค่าความแข็ง หลังจากนั้นก็เว้นระยะการวัดห่างมากขึ้นเป็นทุกๆ 10 มม. |
5. นำไปสร้างกราฟแสดงความสัมพันธ์ระหว่างค่าความแข็งและระยะจากปลายแท่งเหล็กก็จะแสดงให้เห็นถึงความสามารถในการชุบแข็งของเหล็กกล้าชนิดนั้น |
|
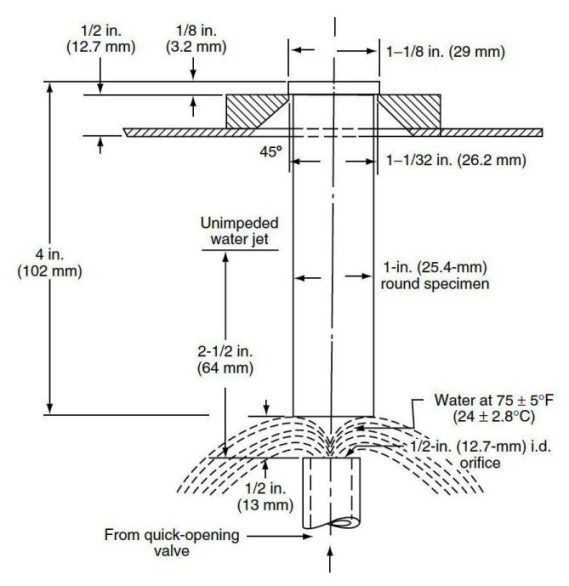 |
ลักษณะของชิ้นงานและการจัดวางการทดสอบ Jominy End Quench Test |
[George E. Totten. Steel Heat Treatment Handbook : Metallurgy and Technologies, CRC Press, USA 2006] |
เนื่องจากการเติมคาร์บอนเข้าไปที่ชั้นผิวนั้นต้องอาศัยการแพร่ของคาร์บอนซึ่งจัดเป็นกระบวนการที่ต้องอาศัยความร้อนและเวลา ดังนั้นจึงต้องทำที่อุณหภูมิสูงเป็นเวลาที่เหมาะสม รวมทั้งต้องควบคุมศักย์คาร์บอนที่ผิวนอกสุดของชิ้นงานเหล็กด้วย ซึ่งโดยปกติศักย์คาร์บอนที่ใช้จะอยู่ที่ 0.8%C ส่วนอุณหภูมิจะอยู่ที่ประมาณ 900-950 องศาเซลเซียส และเวลาประมาณ 4-8 ชั่วโมง ขึ้นกับความหนาของชั้นผิวแข็งที่ต้องการ
|
|
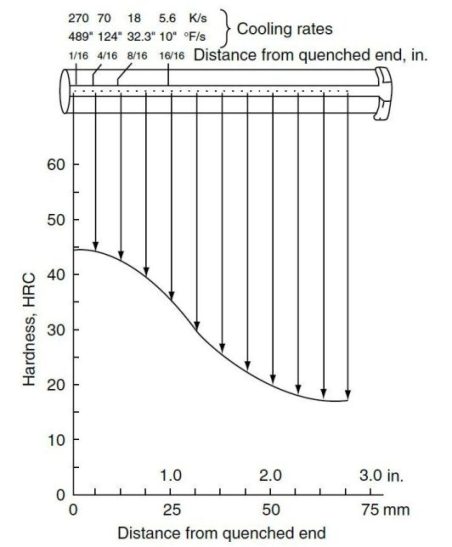 |
ตำแหน่งการวัดความแข็งรอกเวลล์ C และพล็อตค่าความแข็งเทียบระยะลึกเข้าไปจากผิวชิ้นงานทดสอบ Jominy End Quench Test |
[George E. Totten. Steel Heat Treatment Handbook : Metallurgy and Technologies, CRC Press, USA 2006] |
|
|
ข้อจำกัดของ Jominy End Quench Test |
|
Jominy End Quench Test ใช้กับเหล็กกล้าคาร์บอนและเหล็กกล้าผสมต่ำ แต่ไม่เหมาะสมกับเหล็กกล้าที่มีความสามารถในการชุบสูงมากๆ เช่น เหล็กกล้าเครื่องมือที่ชุบแข็งโดยการเย็นตัวในอากาศได้ เนื่องจากชิ้นงาน Jominy เองก็เกิดการถ่ายเทความร้อนออกตามแนวรัศมีด้วย โดยเฉพาะบริเวณที่ห่างจากปลายก็จะยิ่งได้รับอิทธิพลของการเย็นตัวอันเนื่องมาจากการถ่ายเทความร้อนทางด้านรัศมี |
|
|
---------------------------------------------- |
การเย็นตัวระหว่างการชุบเย็นด้วยสารชุบ |
|
เมื่อชุบชิ้นงานที่มีอุณหภูมิสูงลงในสารชุบ ความร้อนจะถ่ายโอนออกจากชิ้นงานสู่สารชุบที่อยู่รอบๆ ส่งผลให้อุณหภูมิของชิ้นงานลดลง โดยทั่วไปแล้วอัตราการเย็นตัวของชิ้นงานที่ชุบลงในสารชุบที่เป็นของเหลวนั้น แบ่งได้เป็น 3 ช่วง ดังนี้ |
|
ช่วงที่ 1 ของเหลวที่อยู่ติดกับผิวชิ้นงานกลายเป็นไอ ทำให้เกิดฟิล์มไอปกคลุมผิวชิ้นงาน ความร้อนถ่ายโอนออกจากชิ้นงานโดยการนำ (conduction) และการแผ่รังสี (radiation) เป็นหลัก แต่การนำความร้อนของไอน้ำนั้นต่ำดังนั้นอัตราการเย็นตัวของชิ้นงานในช่วงแรกจึงไม่สูงมากนัก |
|
ช่วงที่ 2 เมื่ออุณหภูมิของชิ้นงานลดลงมาระดับหนึ่ง ฟิล์มไอจะไม่เสถียรและหายไป ดังนั้นของเหลวจะเข้าไปสัมผัสกับชิ้นงานและชิ้นงานถ่ายโอนความร้อนปริมาณมากสู่สารชุบทำให้เกิดการเดือดรุนแรง อัตราการเย็นตัวในช่วงนี้จะสูงที่สุด |
|
ช่วงที่ 3 เมื่อผิวชิ้นงานมีอุณหภูมิเท่ากับจุดเดือดของสารชุบ การเดือดจะสิ้นสุดลง ไม่มีการเดือดและการกลายเป็นไออีกต่อไป การเย็นตัวของชิ้นงานอาศัยการนำความร้อนและการพาความร้อนโดยของเหลวเป็นหลัก |
|
|
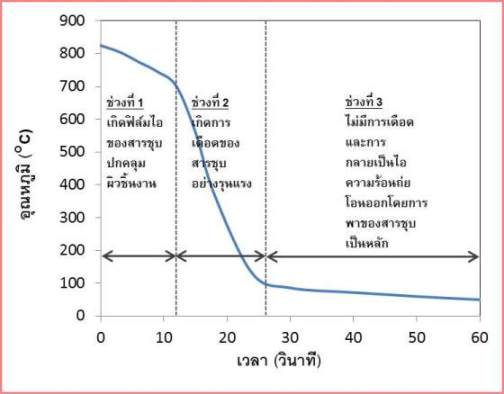 |
อัตราการเย็นตัวของผิวชิ้นงานระหว่างการชุบในสารชุบเหลว |
|
---------------------------------------------- |
|
การระบุความสามารถในการชุบแข็งตามแนวคิดของกรอสแมน |
|
วิธีการทดสอบหาความสามารถในการชุบแข็งอีกแบบหนึ่งซึ่งเป็นแนวคิดของ Grossmann โดยเป็นการนำเอาเหล็กกล้าทรงกระบอกที่มีขนาดเส้นผ่านศูนย์กลางต่างๆ มาชุบในสารชุบภายใต้สภาวะการชุบที่สนใจ หลังจากนั้นผ่าแท่งเหล็กดังกล่าวเพื่อตรวจสอบหาปริมาณมาร์เทนไซต์ที่จุดกึ่งกลางหน้าตัดทรงกระบอก ถ้าที่จุดกึ่งกลางนั้นมีมาร์เทนไซต์อยู่ 50% ก็จะกำหนดให้เส้นผ่านศูนย์กลางของแท่งเหล็กดังกล่าวเป็นค่าเส้นผ่านศูนย์กลางวิกฤต (Dcrit) |
|
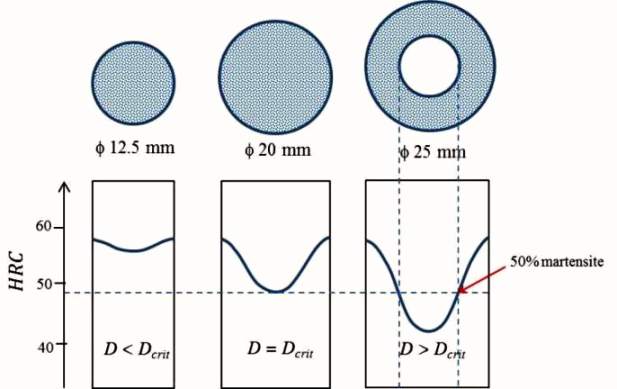 |
การกำหนดค่าเส้นผ่านศูนย์กลางวิกฤต |
|
เนื่องจากชนิดสารชุบและสภาวะการชุบที่เปลี่ยนไปก็จะทำให้ค่า Dcrit เปลี่ยนไป ดังนั้น Grossmann จึงกำหนดความรุนแรงของการชุบขึ้นมาในรูปของสัมประสิทธิ์การถ่ายโอนความร้อนออกจากชิ้นงาน (H) โดยค่า H นี้แสดงคร่าวๆ ในตาราง |
|
|
ตารางค่าสัมปรสิทธิ์การถ่ายโอนความร้อนระหว่างการชุบเย็น [George E. Totten. Steel Heat Treatment Handbook : Metallurgy and Technologies, CRC Press, USA 2006] |
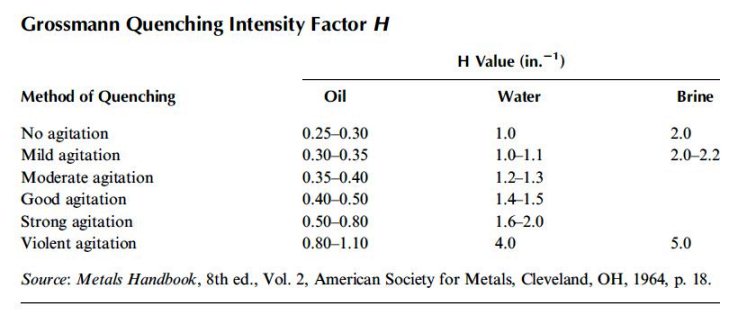 |
|
เพื่อที่จะพิจารณาความสามารถในการชุบโดยยกเว้นผลของความรุนแรงในการชุบ Grossmann จึงกำหนดขนาดเส้นผ่านศูนย์กลางในอุดมคติ (DI) ขึ้นมา โดยให้ค่าสัมประสิทธิ์การถ่ายโอนความร้อนออกจากชิ้นงานโดยการชุบนั้นมีค่ามากจนเข้าสู่อนันต์ (H = ∞) ดังนั้นผิวเหล็กที่สัมผัสโดยตรงกับสารชุบถือว่าเย็นตัวลงจนมีอุณหภูมิเท่ากับอุณหภูมิของสารชุบอย่างทันทีทันใด ( tsurface= 0 ) และขนาดเส้นผ่านศูนย์กลางของแท่งเหล็กทรงกระบอกที่ชุบแล้วได้มาร์เทนไซต์ 50% ณ จุดกึ่งกลางแท่ง ก็คือ DI |
|
สำหรับการชุบที่ค่า H น้อยกว่าในอุดมคติ (ความรุนแรงของการชุบลดลง) Grossmann ได้สร้างแผนภาพที่ใช้แสดงขนาด Dcrit ที่เทียบเท่ากับ DI ไว้ดังแสดงตัวอย่างในภาพ ดังนั้นหากเราทราบ DI ก็จะสามารถหา Dcrit ของการชุบด้วยความรุนแรงในการชุบที่แตกต่างกันออกไป |
|
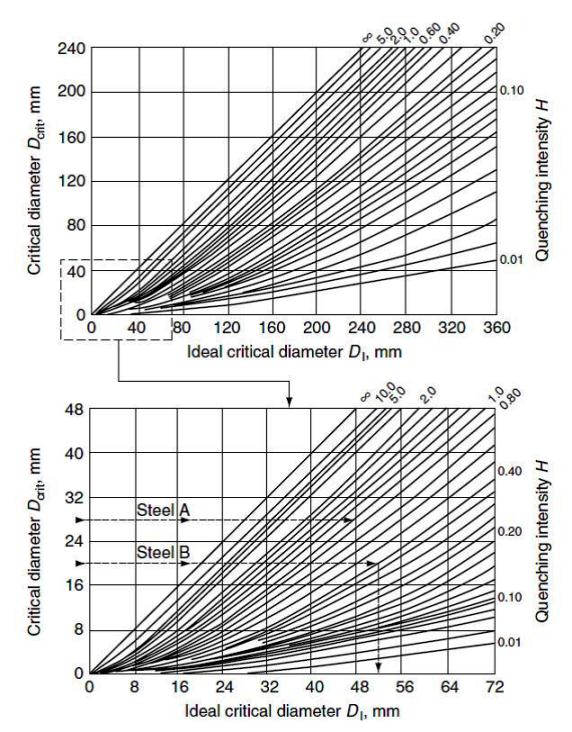 |
แผนภาพแสดงขนาด Dcrit ที่เทียบเท่ากับ DI ภายใต้การชุบเย็นด้วยความรุนแรงในการชุบต่างๆ |
[George E. Totten. Steel Heat Treatment Handbook : Metallurgy and Technologies, CRC Press, USA 2006] |
|
DI ขึ้นกับส่วนผสมทางเคมีของเหล็กและขนาดเกรนของออสเทนไนต์ด้วย จากมาตรฐาน ASTM และ SAE นั้นให้พิจารณาเฉพาะผลของปริมาณคาร์บอนกับขนาดเกรนก่อน แล้วค่อยนำไปคูณกับตัวคูณ (multiplier factor, Mi)ซึ่งเป็นค่าเฉพาะของชนิดธาตุผสมอื่นๆ และขึ้นกับส่วนผสมทางเคมีด้วย ดังนั้นหา DI ในหน่วยนิ้ว ได้จากผลคูณของตัวคูณทั้งหมด ยกตัวอย่างเช่น เหล็กกล้า AISI4140 (SCM440) ซึ่งมีส่วนผสมทางเคมี คือ 0.40%C, 0.8%Mn, 0.25%Si, 1.0%Cr, 0.2%Mo ขนาดเกรนตามมาตรฐาน ASTM คือ เบอร์ 7 หาตัวคูณมาจากตารางที่ 6 ในมาตรฐาน ASTM A255 – 10 หากมีการเติมโบรอนในเหล็กก็ต้องเพิ่มการพิจารณาผลของโบรอนเพิ่มอีกต่างหากด้วยเนื่องจากโบรอนเพียงเล็กน้อยเพิ่มความสามารถในการชุบแข็งได้มาก อย่างไรก็ตามกรณีที่มีโบรอนนั้น ขอไม่กล่าวถึงในที่นี้ |
|
DI = MC x MMn x MSi x MCr x MMo = 0.22 x 3.667 x 1.175 x 3.16 x 1.6 = 4.8 นิ้ว หรือ 120 มิลลิเมตร |
|
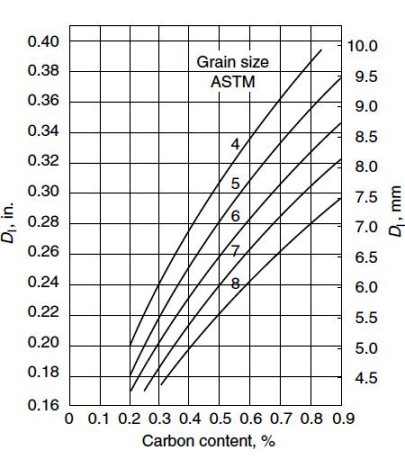 |
แผนภาพแสดงขนาด DI ซึ่งขึ้นกับเปอร์เซ็นต์คาร์บอนและขนาดเกรนของออสเทนไนต์ DI ภายใต้การชุบเย็นด้วยความรุนแรงในการชุบต่างๆ |
[George E. Totten. Steel Heat Treatment Handbook : Metallurgy and Technologies, CRC Press, USA 2006] |
|
ค่า DI ที่ได้นั้นหากนำไปหาเป็น Dcrit ก็ให้พิจารณาว่าจะเลือกความรุนแรงในการชุบอย่างไร เช่น ถ้าเป็นการชุบในน้ำมันที่มีการหมุนเวียนเล็กน้อย (หรือมีการแกว่งตัวงานเบาๆ) ค่า H อยู่ที่ประมาณ 0.3 ดังนั้น Dcrit ประมาณ 60 มิลลิเมตร (นั่นคือประมาณการได้ว่าจะมีมาร์เทนไซต์ 50% ที่จุดกึ่งกลางแท่งทรงกระบอกขนาดเส้นผ่านศูนย์กลาง 60 มิลลิเมตร) |
|
สรุบขั้นตอนการใช้แผนภาพของ Grossman แบบง่ายๆ คือ |
|
1. หา DI จากส่วนผสมทางเคมีของเหล็กและขนาดเกรน |
|
2. หาค่า H ของรูปแบบการชุบที่ใช้ (ผู้ผลิตและจำหน่ายสารชุบสามารถให้ข้อมูลนี้ได้) |
|
3. อ่านค่า Dcrit |
|
---------------------------------------------- |
|
|
ผลกระทบของขนาดชิ้นงาน (Mass Effect) |
|
ขนาดของชิ้นงานมีผลต่ออัตราการเย็นตัวด้วยเช่นกัน เนื่องจากความร้อนถ่ายโอนออกจากชิ้นงานได้มากและเร็วผ่านผิวของชิ้นงาน ดังนั้นอัตราส่วนระหว่างผิวต่อปริมาตรของชิ้นงานที่แตกต่างกัน ก็จะส่งผลให้อัตราการเย็นตัวแตกต่างกัน และอาจทำให้ความแข็งผิวหลังชุบแตกต่างกันโดยเฉพาะถ้าเหล็กกล้านั้นมีความสามารถในการชุบแข็งต่ำ นอกจากนี้ยังส่งผลให้มีความเค้นตกค้างในชิ้นงานที่แตกต่างกันด้วย |
|
การทดลองที่จะทำให้เห็นถึงผลกระทบของขนาดชิ้นงานนั้นสามารถทำได้ง่ายในห้องทดลอง รวมไปถึงในอุตสาหกรรมเช่นกัน ยกตัวอย่าง เช่น การนำแท่งเหล็กคาร์บอน AISI 1045 หรือ JIS S45C รูปทรงกระบอกยาวที่มีขนาดหน้าตัดแตกต่างกันตั้งแต่ 0.5 – 4 นิ้ว มาอบให้เป็นออสเทนไนต์โดยใช้อุณหภูมิและเวลาในการอบแต่ละชิ้นเท่าๆ กัน จากนั้นชุบลงในสารชุบด้วยสภาพการชุบเดียวกัน เมื่อนำชิ้นงานไปตรวจสอบค่าความแข็งที่ผิวของชิ้นงานจะพบว่ามีค่าความแข็งไม่เท่ากัน เนื่องจากอัตราการเย็นตัวที่ผิวนั้นลดลงตามขนาดหน้าตัดที่ใหญ่ขึ้นและเหล็กกล้าชนิดนี้มีความสามารถในการชุบแข็งต่ำ อัตราการเย็นตัวโดยการชุบที่ช้าลงส่งผลกระทบรุนแรงต่อโครงสร้างจุลภาคที่ได้หลังการชุบและทำให้ความแข็งผิวหลังชุบแตกต่างกัน การพิจารณาผลกระทบของขนาดชิ้นงานนี้สามารถแสดงโดยอาศัยการพล็อตความแข็งเทียบระยะลึกจากผิวของชิ้นงานที่มีขนาดหน้าตัดแตกต่างกัน หรือเรียกว่า Hardness-Penetration Profile |
|
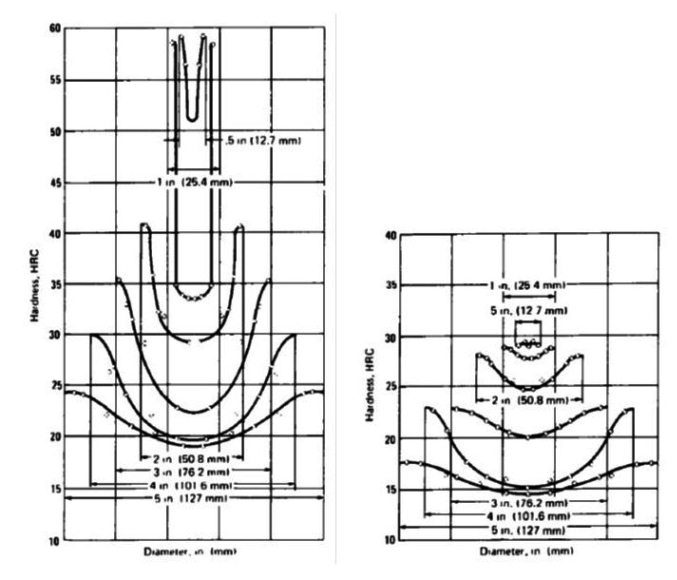 |
ความแข็งที่ตำแหน่งต่างๆ ตลอดหน้าตัดชิ้นงานเหล็กกล้า AISI 1045 (JIS S45C) รูปร่างทรงกระบอกขนาดต่างๆ ซ้าย-ชุบในน้ำ และ ขวา-ชุบในน้ำมัน |
[Heat Treater’s Guide: Practice and Procedure for Iron and Steel. ASM International 2nd edition, USA 1995] |
|
อ้างอิง |
|
[1] George E. Totten. Steel Heat Treatment Handbook : Metallurgy and Technologies, CRC Press, USA 2006 |
[2] Heat Treater’s Guide: Practice and Procedure for Iron and Steel. ASM International 2nd edition, USA 1995 |
[3] ASTM A255-10 "Standard Test Methods for Determining Hardenability of Steel"ASTM International, West Conshohocken, PA, 2010, DOI: 10.1520/A0255-10, www.astm.org |
|